Tony
Staff member
I was having some issues with quick prints slipping on the drive gear. On the stock Ender 3 Pro (and likely most Ender's), there is what looks like a 64 pitch pinion gear that pinches the filament between the gear and a roller bearing. As stated, I was getting some slipping as it is only being driven from one side. So, I thought this would be an "upgrade". I was wrong...
The idler gear physically digs into the carrier base and grabs hard enough to actually bind up the stepper motor and cause it to stop feeding. Below is a picture of the carrier where it has dug a gouge in the aluminum anodizing. Yes, I can file the gear, and it will likely work just fine, but this is not the worst flaw of this design. But I thought if you can pinch the filament between two drive rollers, my feed issues will be solved. Well, that would be true IF it was not destroying itself because they don't know how to machine a flat surface on the idler gear, or provide a thin thrust washer under it to keep it off the carrier.
Now lets talk about the bearing and the bolt that hold the idler gear. It has two very small needle bearings and just a regular fully threaded bolt. So the threads are what the needle bearings are riding on, not a smooth surface. Is this a bad thing? Not really with the load it has however it does come with a very strong spring which does put much more pressure on these bearings since they are only touching a thread, not a shaft.
So far, the force of the strong spring that it comes with will eventually destroy the needle bearings that should ride on a pin, and the idler gear is digging into the carrier stopping the feed of filament. Nice.
The next part I do not have a picture to compare, however the drive gear surface per revolution is about 25% or more SMALLER than the stock gear. This means you need to go in and have it extrude more just to keep up to what it should be. This is an issue in the touch screen I purchased as the menu that I "think" is for this, resets every time you turn off the printer. So the best way to do this would be to figure out a feed speed for the filament to extrude the correct amount in your slicer. Of course this is not that hard to do, just takes time in test prints to get it right, but even on the product page it stated they had to raise the feed up by 39%.
So the feed is not that big of a deal, but paying for something that is supposed to be a completed unit (finished product) and having to modify it and purchase extra items that should have come with it is just not a "Finished Product" IMO.
If you are willing to file the gear, find a small plastic washer or something (like from an electric Rc motor shaft....) and use a proper pin (you can drill and tap for a set screw to hold the pin in right next to the hole, pretty easy, unless you break the tap lol), then go ahead and get it. It looks fantastic, is all aluminum, has a better coupler for the bowden tube and it does in fact drive from both sides of the filament with more aggressive teeth and has a stronger spring.
I am one of those people that can over come this issue, as I assume most others with a 3D printer are as well. But if you are not, just know the issues that could pop up going into it and be ready.
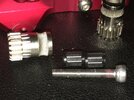
The idler gear physically digs into the carrier base and grabs hard enough to actually bind up the stepper motor and cause it to stop feeding. Below is a picture of the carrier where it has dug a gouge in the aluminum anodizing. Yes, I can file the gear, and it will likely work just fine, but this is not the worst flaw of this design. But I thought if you can pinch the filament between two drive rollers, my feed issues will be solved. Well, that would be true IF it was not destroying itself because they don't know how to machine a flat surface on the idler gear, or provide a thin thrust washer under it to keep it off the carrier.
Now lets talk about the bearing and the bolt that hold the idler gear. It has two very small needle bearings and just a regular fully threaded bolt. So the threads are what the needle bearings are riding on, not a smooth surface. Is this a bad thing? Not really with the load it has however it does come with a very strong spring which does put much more pressure on these bearings since they are only touching a thread, not a shaft.
So far, the force of the strong spring that it comes with will eventually destroy the needle bearings that should ride on a pin, and the idler gear is digging into the carrier stopping the feed of filament. Nice.
The next part I do not have a picture to compare, however the drive gear surface per revolution is about 25% or more SMALLER than the stock gear. This means you need to go in and have it extrude more just to keep up to what it should be. This is an issue in the touch screen I purchased as the menu that I "think" is for this, resets every time you turn off the printer. So the best way to do this would be to figure out a feed speed for the filament to extrude the correct amount in your slicer. Of course this is not that hard to do, just takes time in test prints to get it right, but even on the product page it stated they had to raise the feed up by 39%.
So the feed is not that big of a deal, but paying for something that is supposed to be a completed unit (finished product) and having to modify it and purchase extra items that should have come with it is just not a "Finished Product" IMO.
If you are willing to file the gear, find a small plastic washer or something (like from an electric Rc motor shaft....) and use a proper pin (you can drill and tap for a set screw to hold the pin in right next to the hole, pretty easy, unless you break the tap lol), then go ahead and get it. It looks fantastic, is all aluminum, has a better coupler for the bowden tube and it does in fact drive from both sides of the filament with more aggressive teeth and has a stronger spring.
I am one of those people that can over come this issue, as I assume most others with a 3D printer are as well. But if you are not, just know the issues that could pop up going into it and be ready.
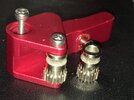
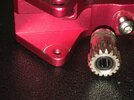
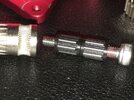
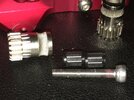
Last edited: