Nose strake and cowl vents. A strake is a piece of metal that is usually longer than it is wide. Depending on what characteristic the designer wants to achieve, it can be mounted on the nose, in front of the wing, or at the rear under the tail cone. The Tutor nose strake helps with flight stabilization. I'm sorry but I forgot to take a lot of pictures.
Pic 1. A rainy day at Base Borden to get a picture and mesurements of a strake. Pic. 2. At home nice and dry on the computer for a head on shot. Hard to see the strakes.
Pic. 3. The strake is installed. Real size is 2" wide x 64" long. 1/8 is 1/4" wide x 8" long. Using pic 1 for a starting point. I leveled the model. Marked the spot where the strake meets the light on the real plane. Took a measurement from the table to that mark. Measured back 8" on the nose and measured up from the table and put a mark at the same height as at the nose. Ran a pencil line between the two marks. Put some masking tape along the pencil line so that you can still see the pencil line. This ia the guide for the hot wire cutter. I set the depth of the hot wire cutter to 1/4" and cut a 1/16" slot 8" long. To get the curve for the strake, I used a piece of cereal box card board 3" x 8".
Pushed the edge of the cardboard into the slot at the nose light. Then traced the curve on to the cardboard. Only got about an inch of line on the cardboard. Used scissors to cut the curve. Put the cardboard back in the slot in the same place. The card board went the 1/4" to the bottom of the slot. This put more of the length of carboard in the slot.
Traced that outline and cut that curve. I did this a bunch of times until the cardboard was touching the bottom of the slot all the way along the 8" slot. Now I took this profile and transferred it to 1/16" plywood. I moved the cardboard up a 1/2" and traced the profile again. I cut the profile out of the plywood. I now had a 1/2" x 8" strake.
1/4" goes into the slot leaving a 1/4' X 8" strake. After test fitting and tweaking with sand paper, I transferred the wooden form to the plywood and cut it out. Before glueing the strakes in, I marked the position of the cowl vents. Then used the hot wire cutter to relieve the foam so that the vents can be flush mount.
Cowl Vent
Pic. 1. Lower vent. Pic. 2. Upper vent. Behind the upper vent is the electronics bay. These vents draw out the warm are and keep the temperature of the bay down. Back in the last century -1950's-, car customizers, used to stamp louvers into the hoods of the cars. When moving, air coming over the hood would draw warm air out of the engine area to help cool the engines. If you enlarge pic 1 or 2, you will see that this is a hood scoop installed upside down with the scoop still facing forward. Now air passing over it will draw warm air out of the bay. Pic. 3. Example of louvers used on cars. Pic. 4. These are 3D printed vents. I made an appointment the lab at our local library to use the 3D printer. I took pc 2 and my measurements with me to the lab. One of the techs worked with me and out came pic4 in plastic. Two hours time and the outragious price of $1.75 I have 4 tutor vents. Because the vents are installed upside down, I used .030 styrene plastic to take up the difference in height. The two plastics glued together nicely using model plane plastic weld glue. When glued in place, I have a nice flush fit. Pic 5. The lower vents are curved just like in pic 1 of the real plane. I had to shim these vents and curve them. This 3D plasic will not bend it breaks. But, if heated it can be formed. When printing this plastic is a liquid at 195 deg F. It can be formed at around 80F. I just happen to have a heat source in that is in that area. ME. Body core temp 98.6F. If a person is in a room at 70F. Skin temp is usually the same or a bit higher. Got out my infared thermometer, pointed at my thumb and squeezed the trigger. 72 and a bit. That will do it.
I shimmed the vent except for the bottom edge. I put my thumb on the lower edge and a bit of pressure. Slowly the edge started to bend. After a few test fits and thumb heat I got a good fit. Shimmed the bottom edge and glued in place. PIC 6 and 7 show the amount of curve. Pic 8 shows the final installation.
Now I'll try and get a video together.
Don
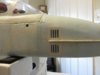